Joint Torque Sensors<em>.</em>
Joint Torque Sensors
KR-JTS (Joint Torque Sensor)
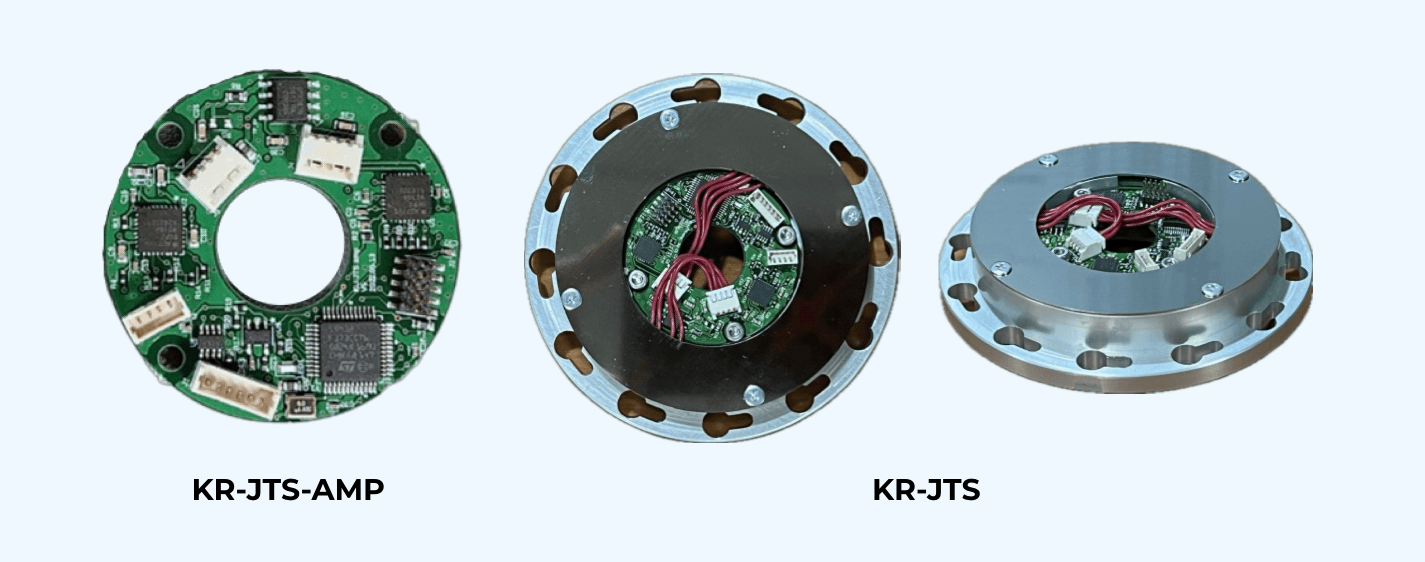
Product overview
- For collision detection, direct teaching, and force control of a robot, it is essential to accurately measure the joint torque transmitted to each link.
- Since torque sensors are installed at every joint of the robot, low torsional stiffness of the sensor tends to reduce the overall stiffness of the robot, leading to degraded position control performance and increased vibration.
- Requirements for ideal torque sensors for robots
1. High torque measurement accuracy
2. Very high torsional stiffness for minimized impact on robot stiffness
3. Low crosstalk for minimized influence of moment or axial loads on torque measurement
4. Thermal stability and long-term reliability
5. Cost-effectiveness
KR-JTS meets all of the above requirements and is recognized as one of the top-performing torque sensors in the market. It offers torsional stiffness 20 to 40 times greater than that of the paired harmonic drive.
Product specifications
Model | JTS-040 | JTS-150 | JTS-250 | JTS-500 | JTS-850 | JTS-1700 | JTS-3800 |
---|---|---|---|---|---|---|---|
Torque capacity(Nm) | 40 | 150 | 250 | 500 | 850 | 1700 | 3800 |
Resolution (Nm) | 0.02 | 0.07 | 0.12 | 0.24 | 0.41 | 0.83 | 1.86 |
Size (mm) | Ø72×14 | Ø75×18 | Ø95×20 | Ø112×20 | Ø135×25 | Ø170×30 | Ø220×40 |
Weight (g) | 78 | 105 | 205 | 300 | 550 | 1100 | 2100 |
JTS stiffness (104Nm/rad) | 36.8 | 81.2 | 100.2 | 185.4 | 434.3 | 1040 | 3150 |
Matching HD HD stiffness (104Nm/rad) |
SHG-14 (0.94) | SHG-20 (25) | SHG-25 (5.0) | SHG-32 (11) | SHG-40 (20) | SHG-50 (40) | RV-120C (202) |
Combined stiffness*(104Nm/rad) | 0.92 (97.8%) | 2.42 (96.8%) | 4.76 (95.2%) | 10.38 (94.4%) | 19.1 (95.5%) | 38.5 (96.2%) | 189.8 (93.9%) |
* The percentage indicates the equivalent combined stiffness when a JTS is added, based on the joint stiffness using only a HD as 100%.